Weed Spraying Rover
An off-road capable mobile robot with accessories for weedwacking and dispensing liquid weed killer controlled with ROS2.
Specifications
Robot:
- 4 AndyMark PG71 gearmotors for propulsion (top speed of about 0.3m/s)
- 4 Brute® 7103500YP 8” x 2” Lawn Mower Drive Wheels for off-road traction and horrible squealing noises when turning on pavement…
- 20mm Aluminum extrusion frame
- Raspberry Pi 5 for robot control with ROS2 Iron Irwini.
- Dual Jaguar (MDL-BDC24) motor controllers with a custom ROS2 driver using a usb to RS232 adapter
- 4 onboard cameras with a Raspberry Pi 5 for video streaming.
- Dedicated Raspberry Pi Pico for arm, weedwacker, and accessory control. (interfaced over USB)
Sprayer:
- 4-DOF robotic arm with 60Kg/cm servos and stepper driven turntable
- Raspberry Pi Pico based arm & accesory controller
- Nozzle, pump, and hose repurposed from a broken battery powered weed spraying wand
- 3D inverse kinematics for precise and intuitive positioning
- Microsoft LifeCam mounted on the end of the arm for sprayer targeting
Weed Wacker:
- Weed wacker mounted on a 40cm folding arm
- Winch deployment
- Direct drive CIM motor for weedwacking with a RYOBI 2-in-1 bladed head on a 3D printed adapter for cutting
- Capable of cutting weeds, grass, small shrubs (and if you aren’t careful, your ankles).
Photo Gallery
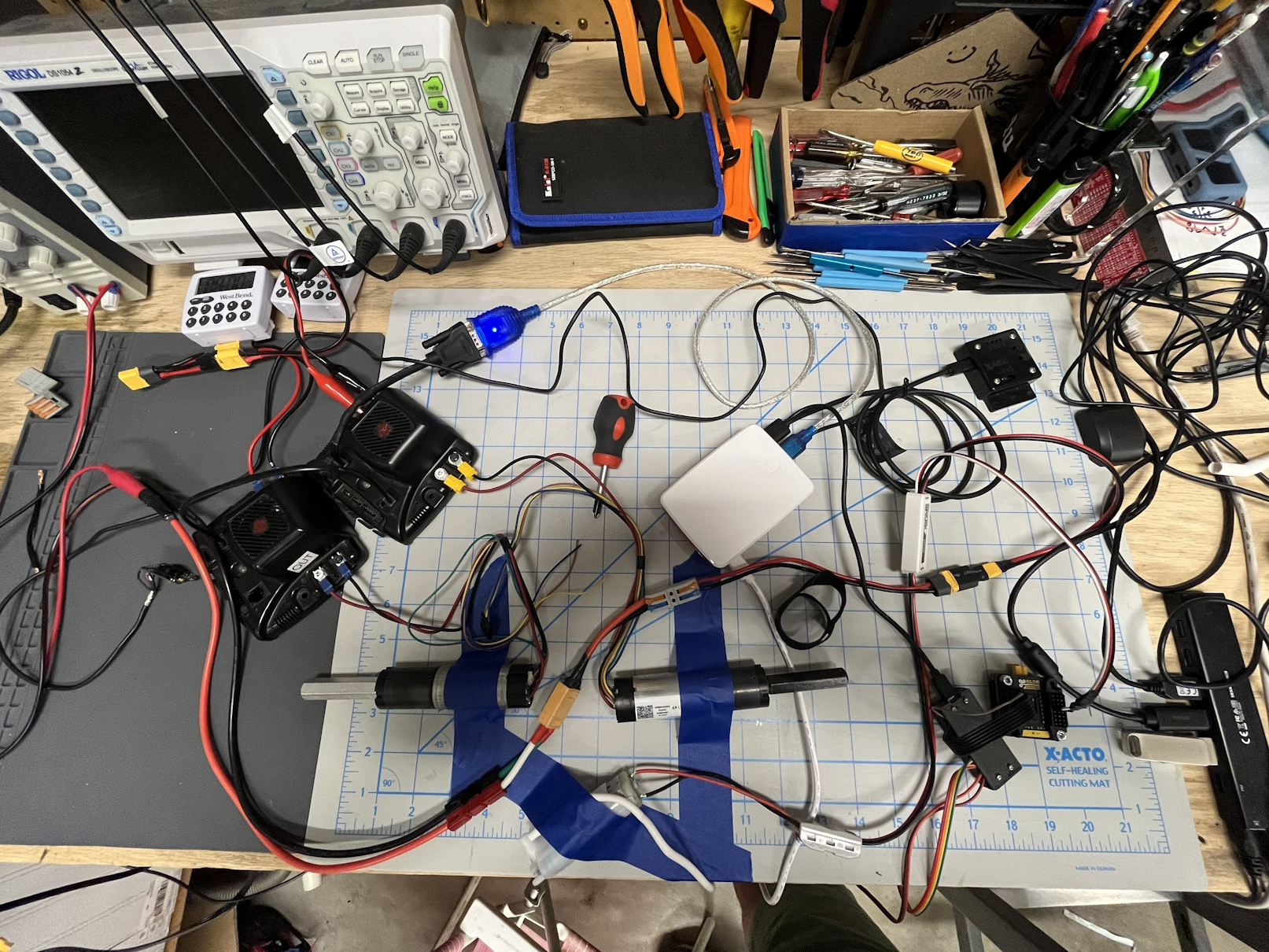
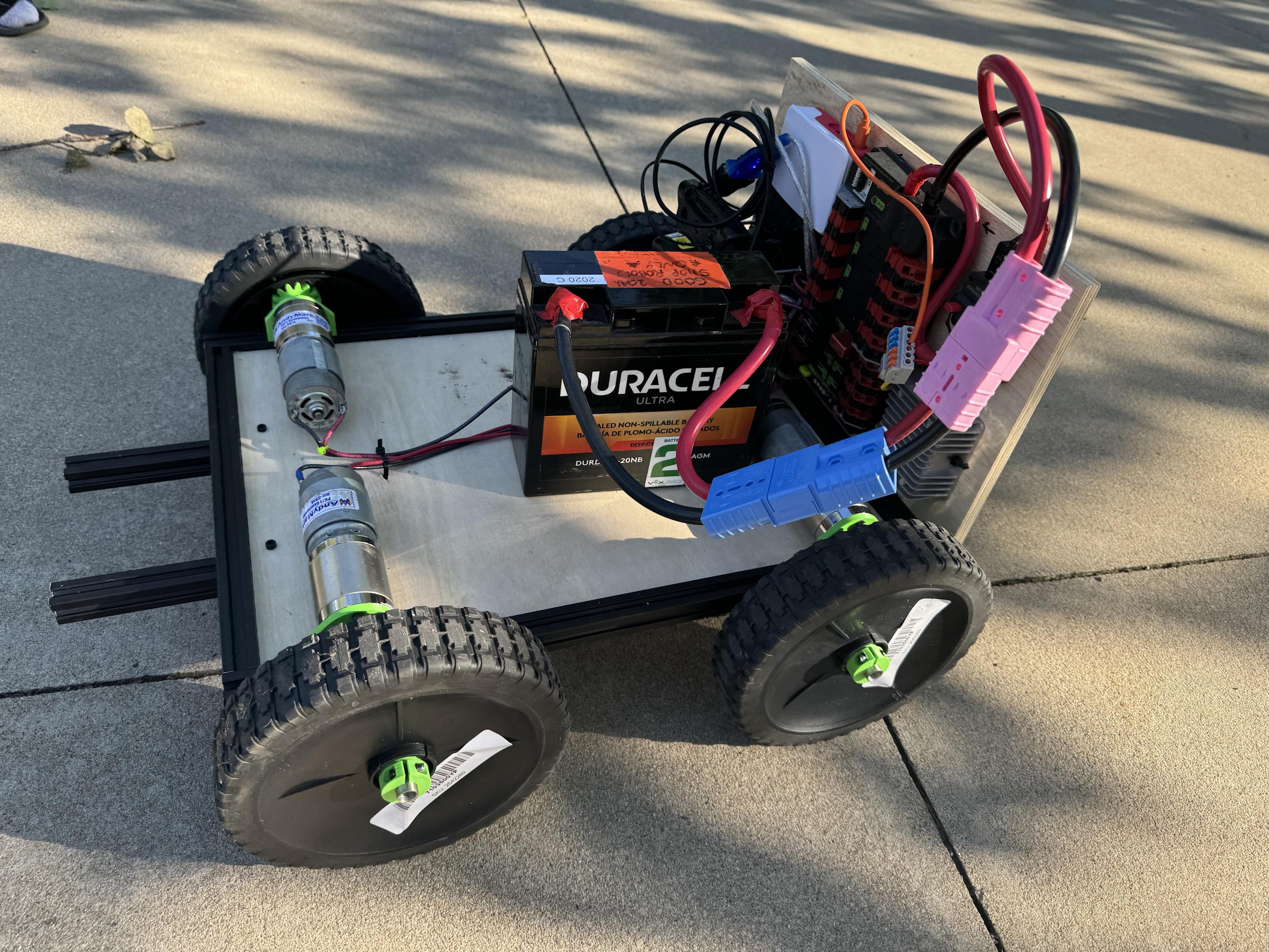
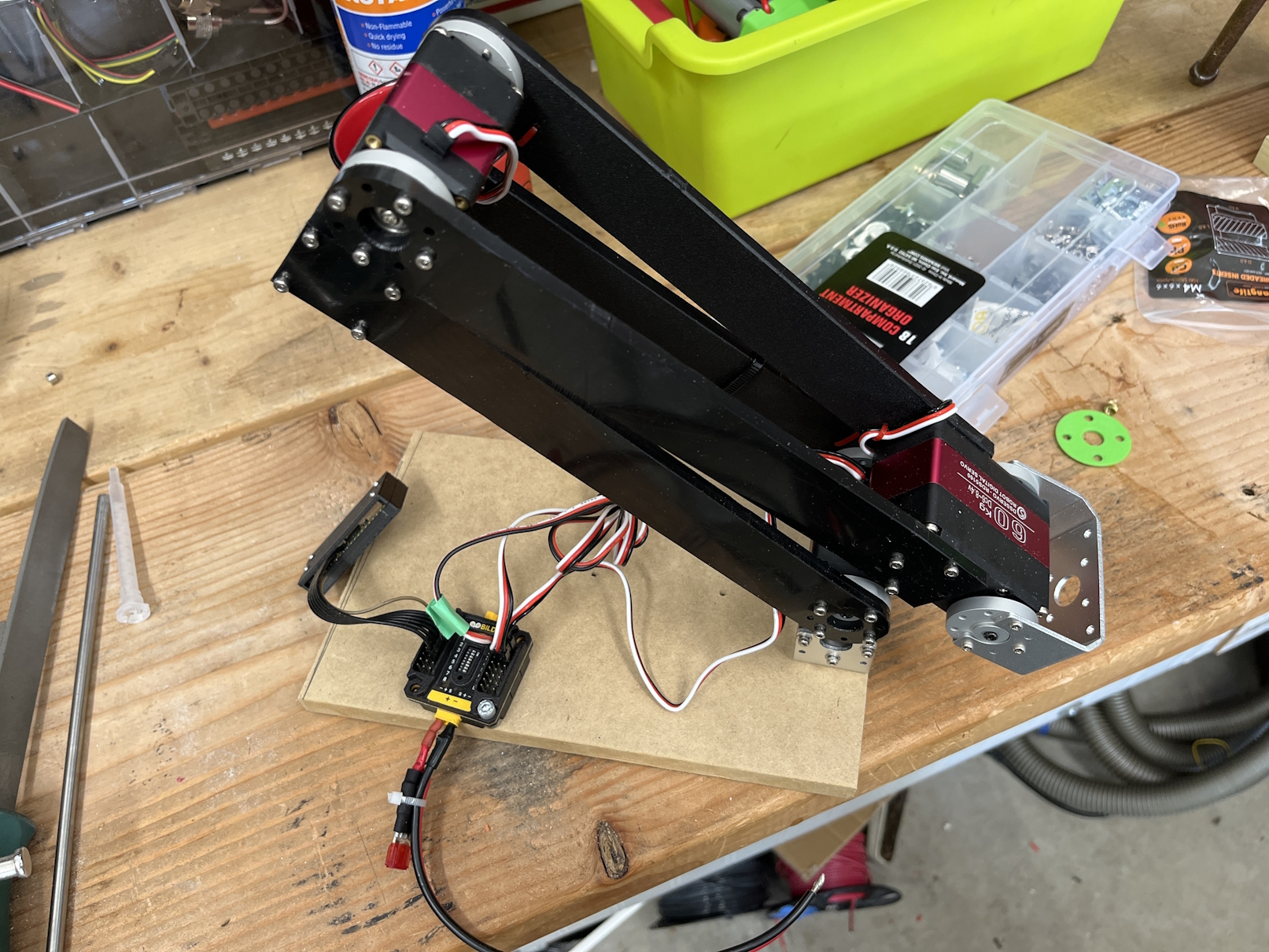
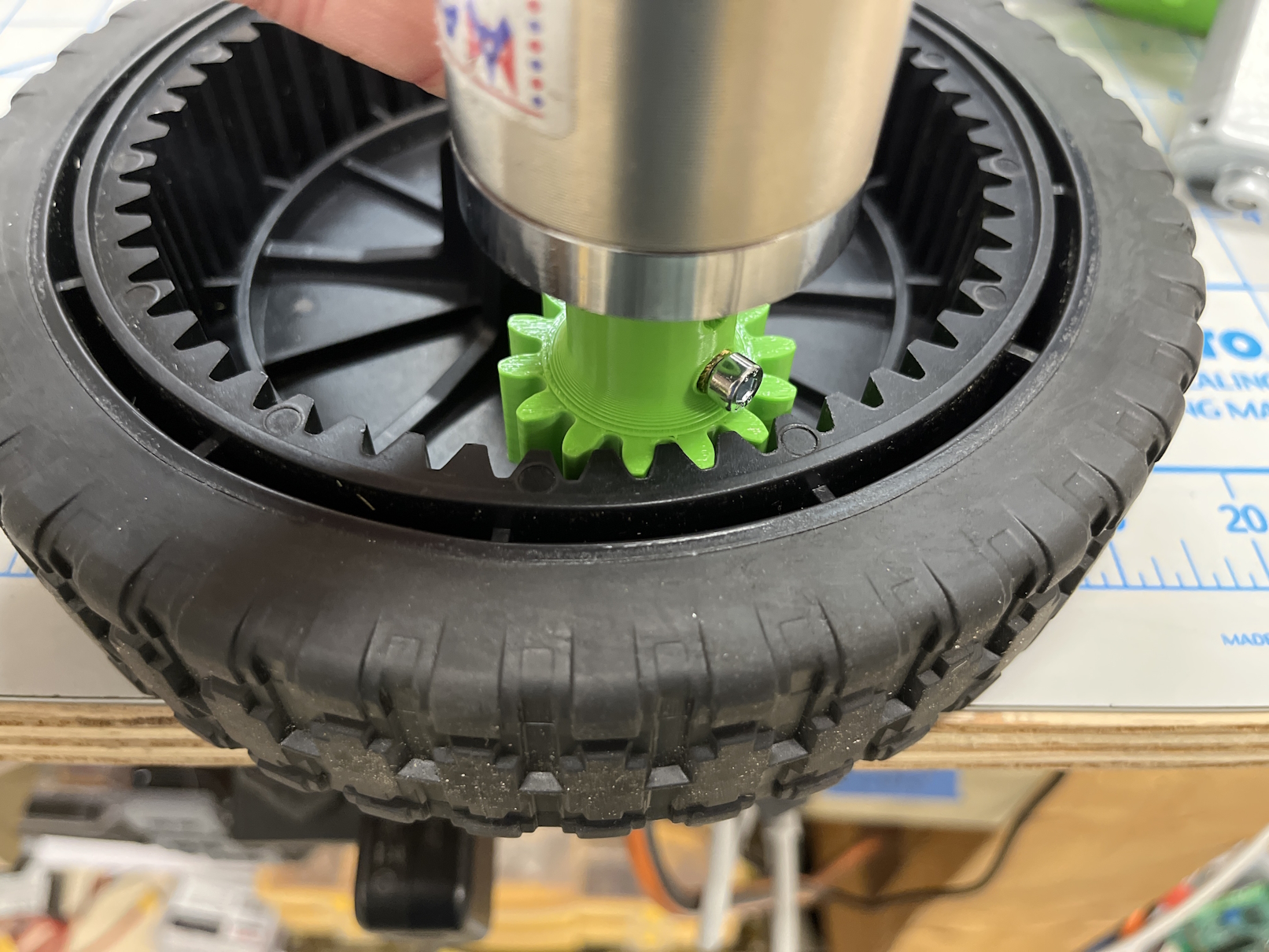
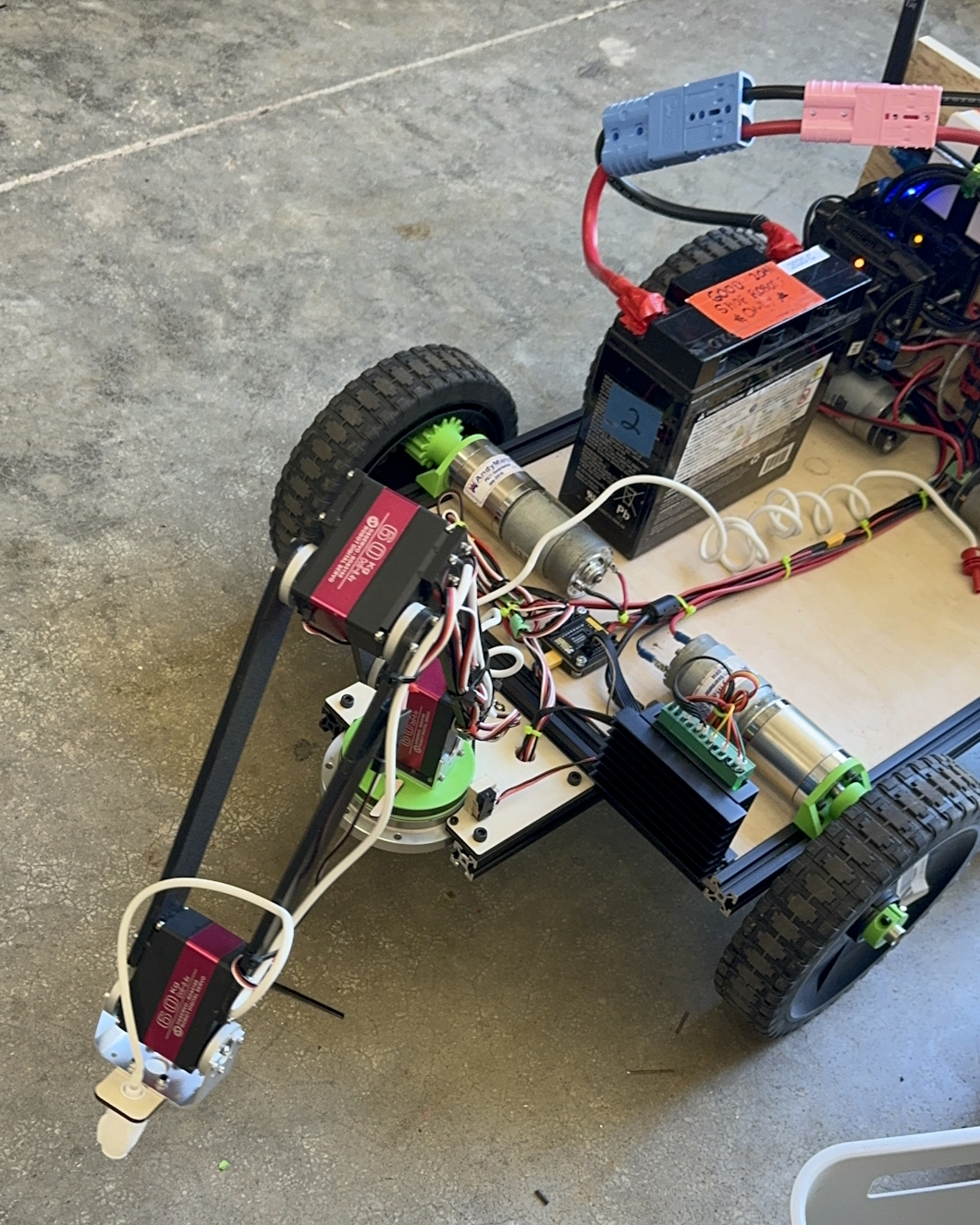

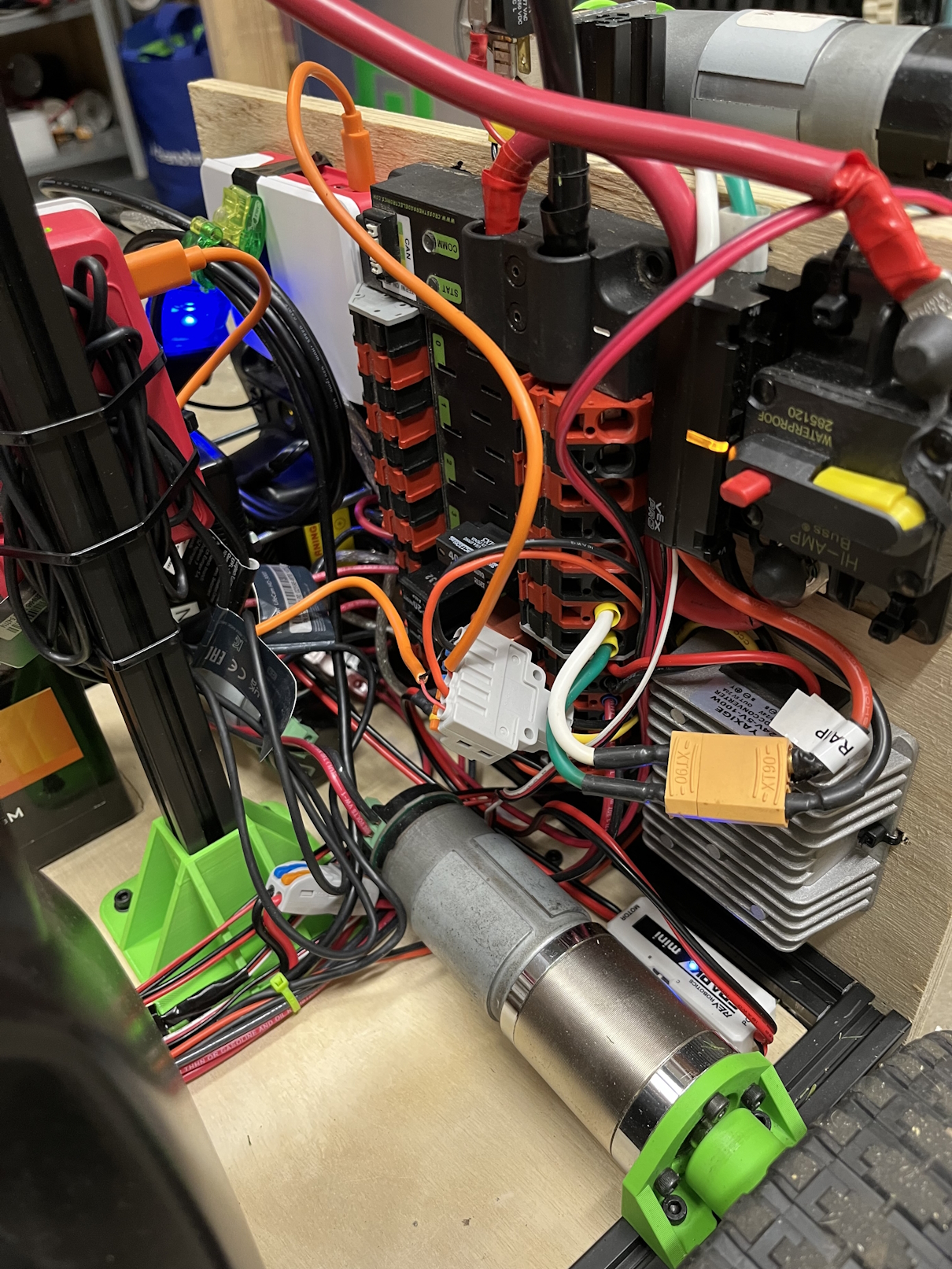
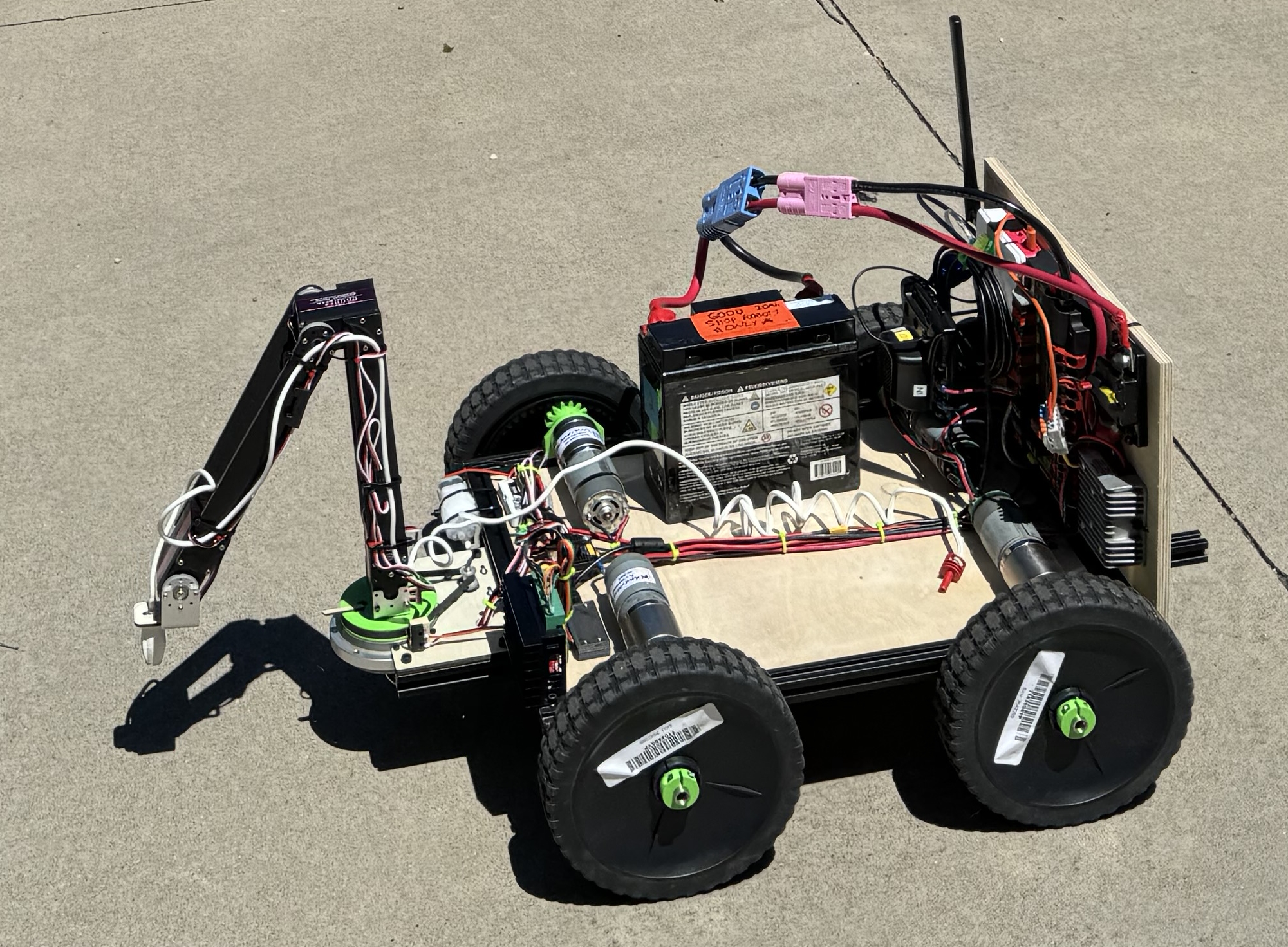
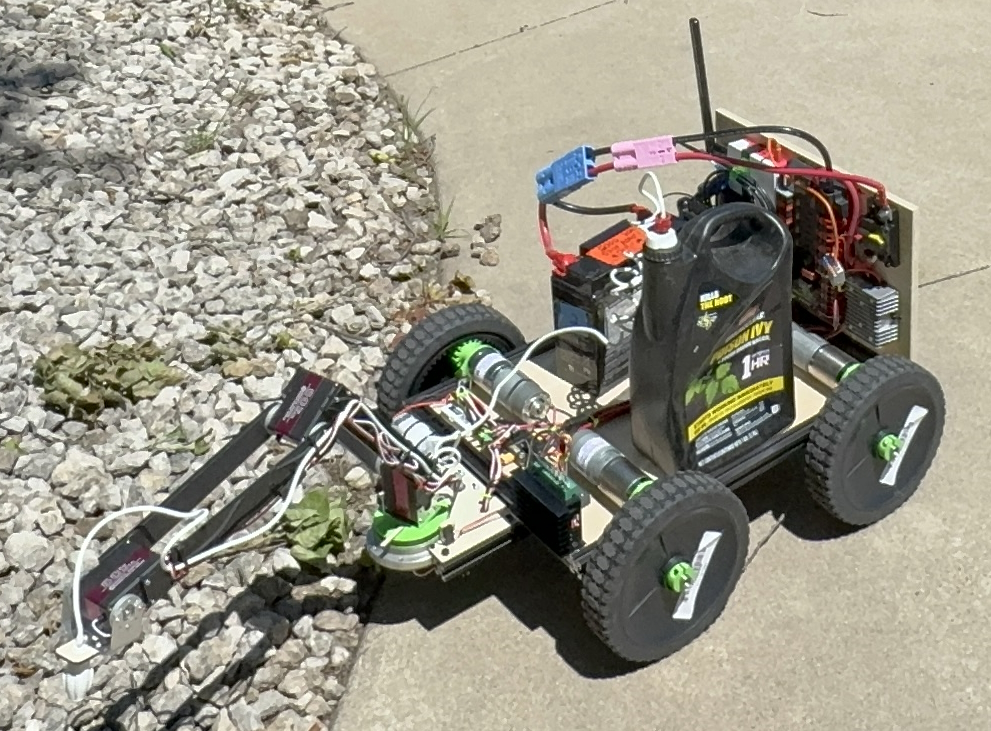
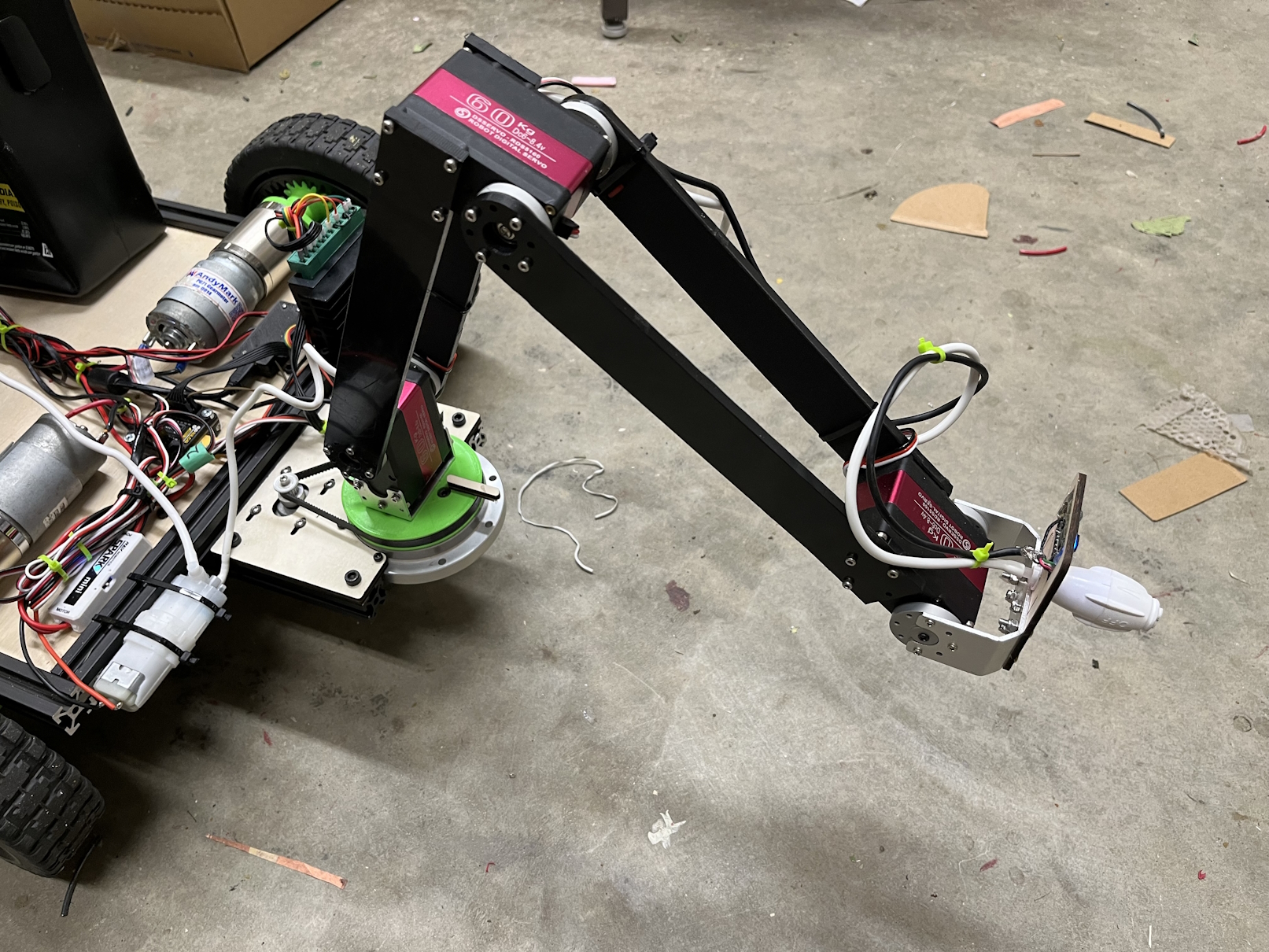
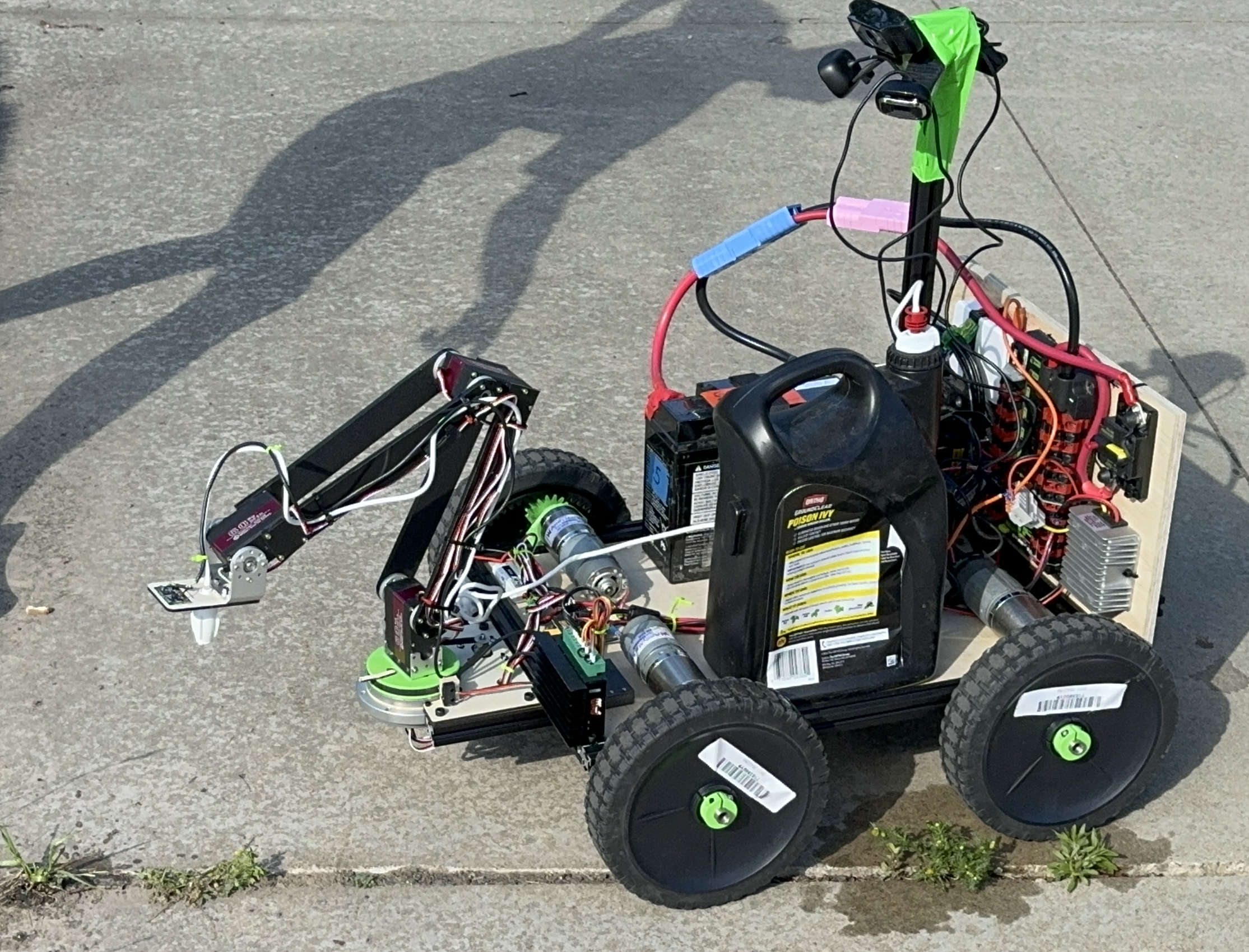
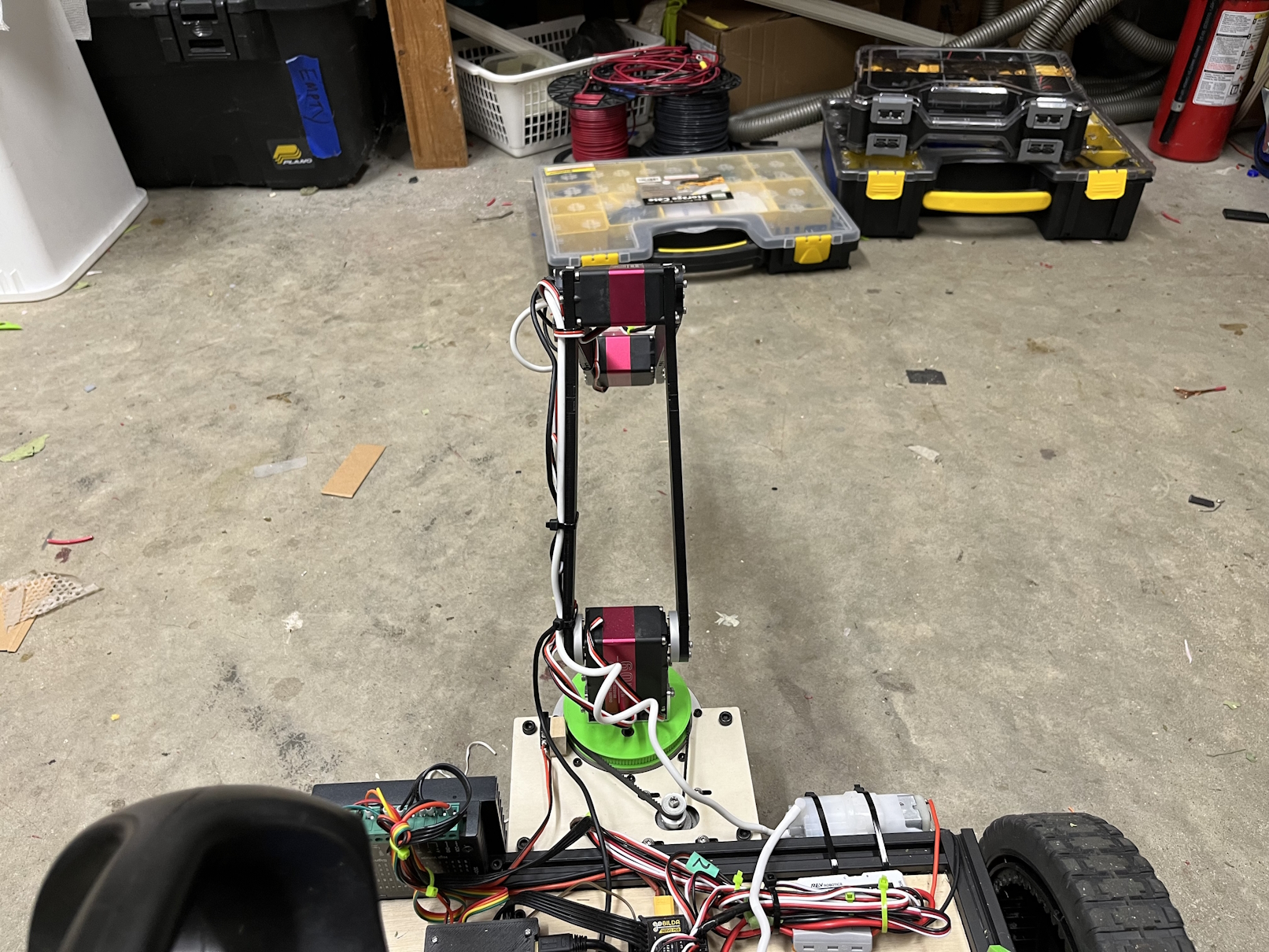
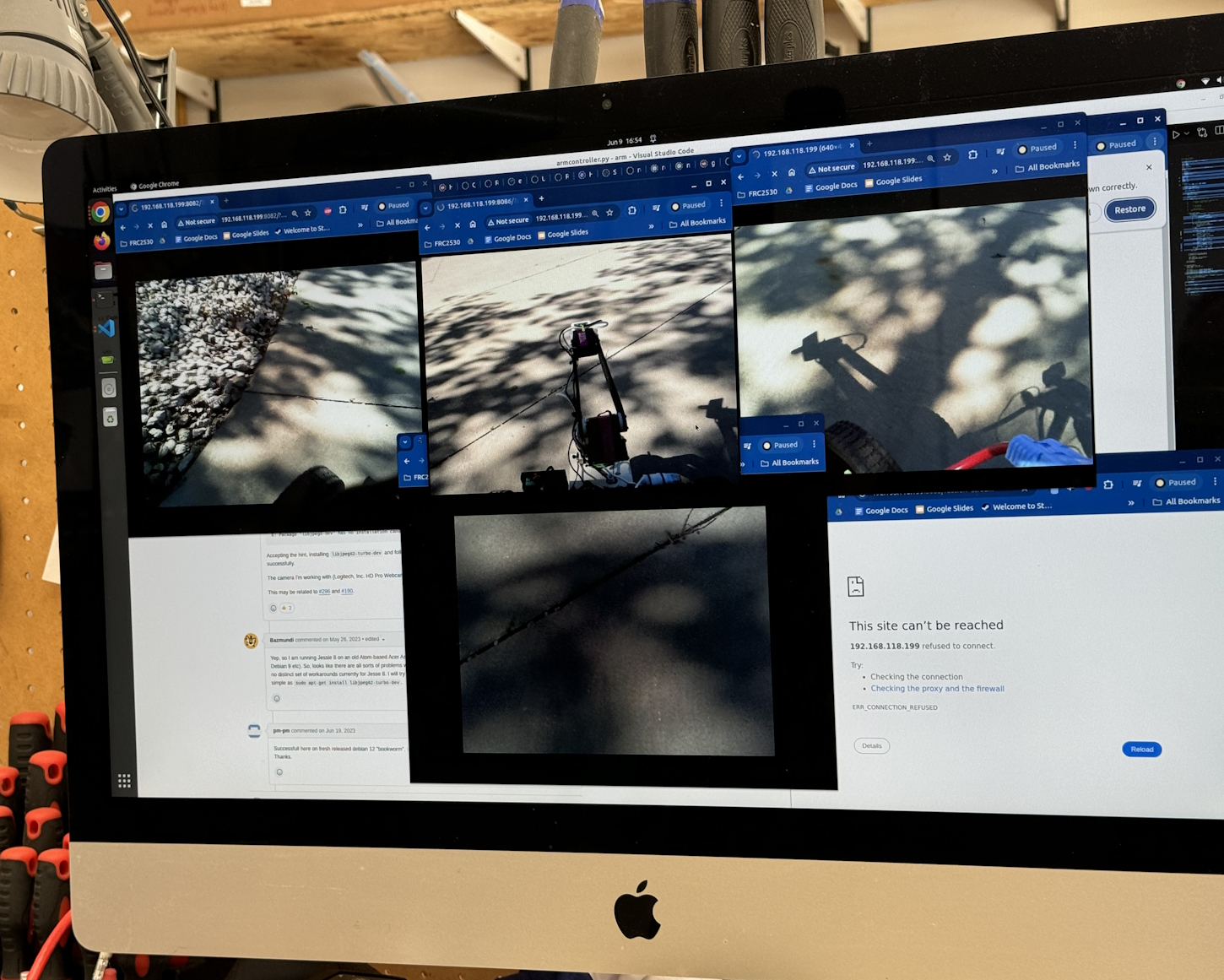
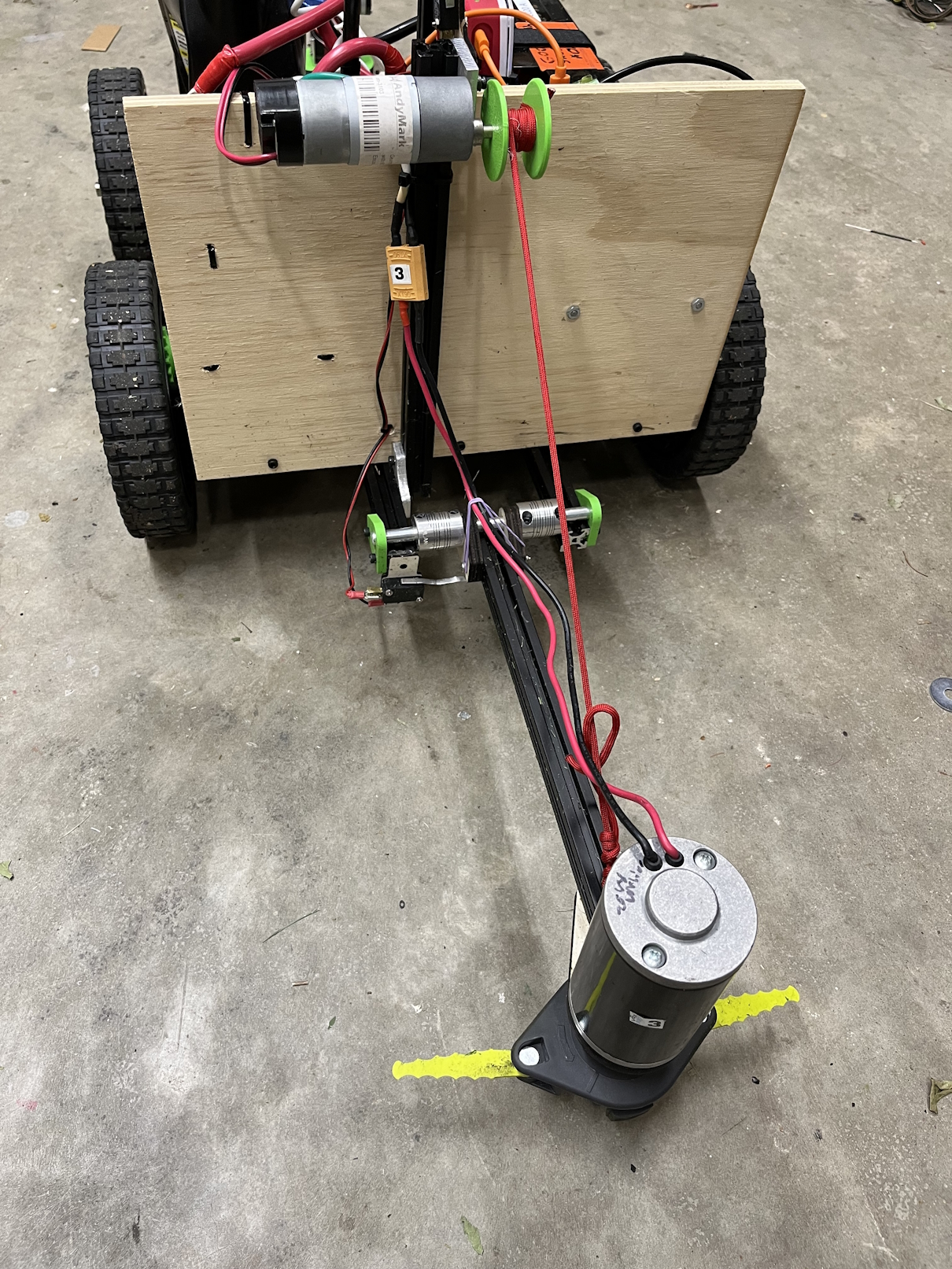
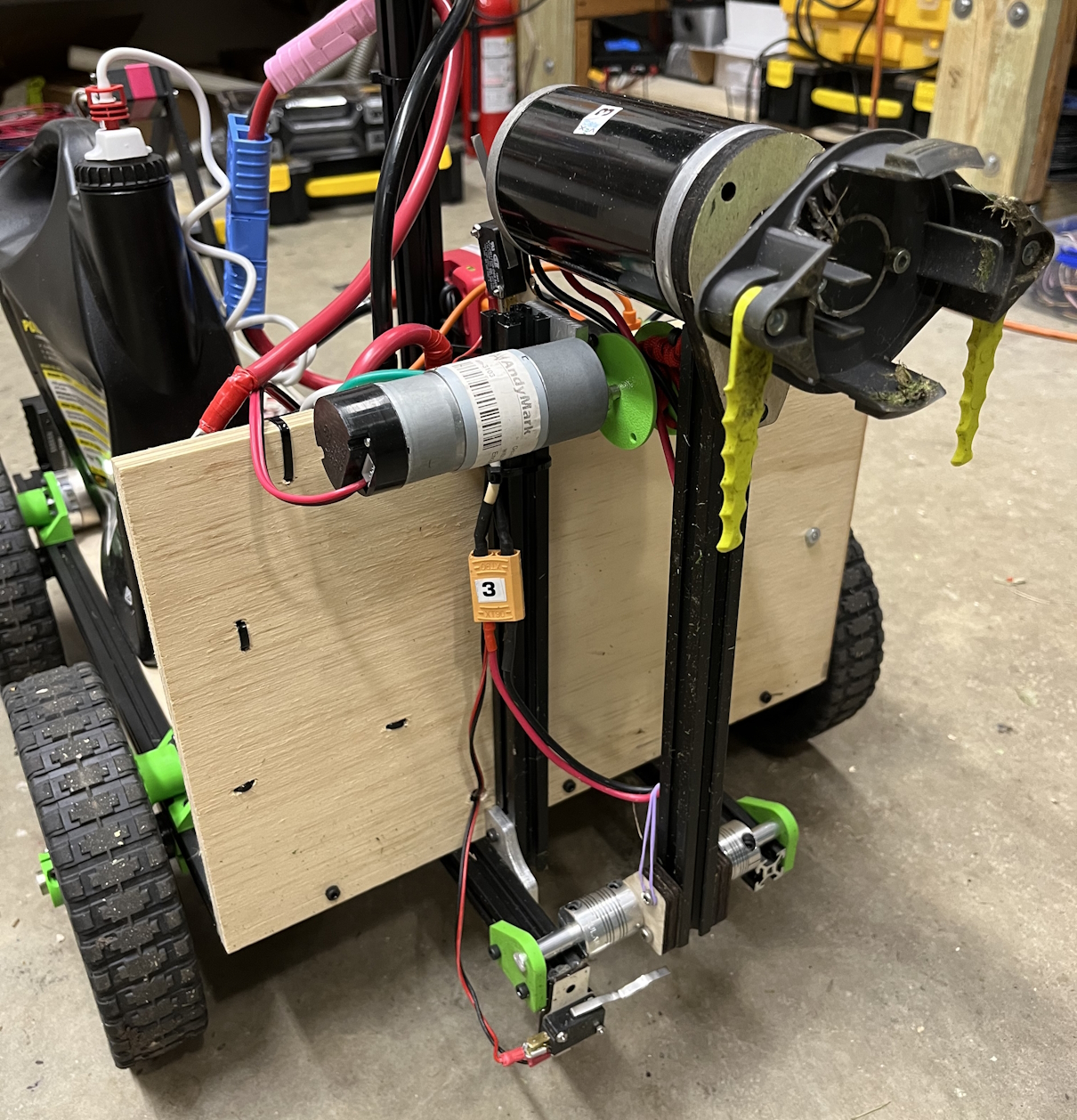
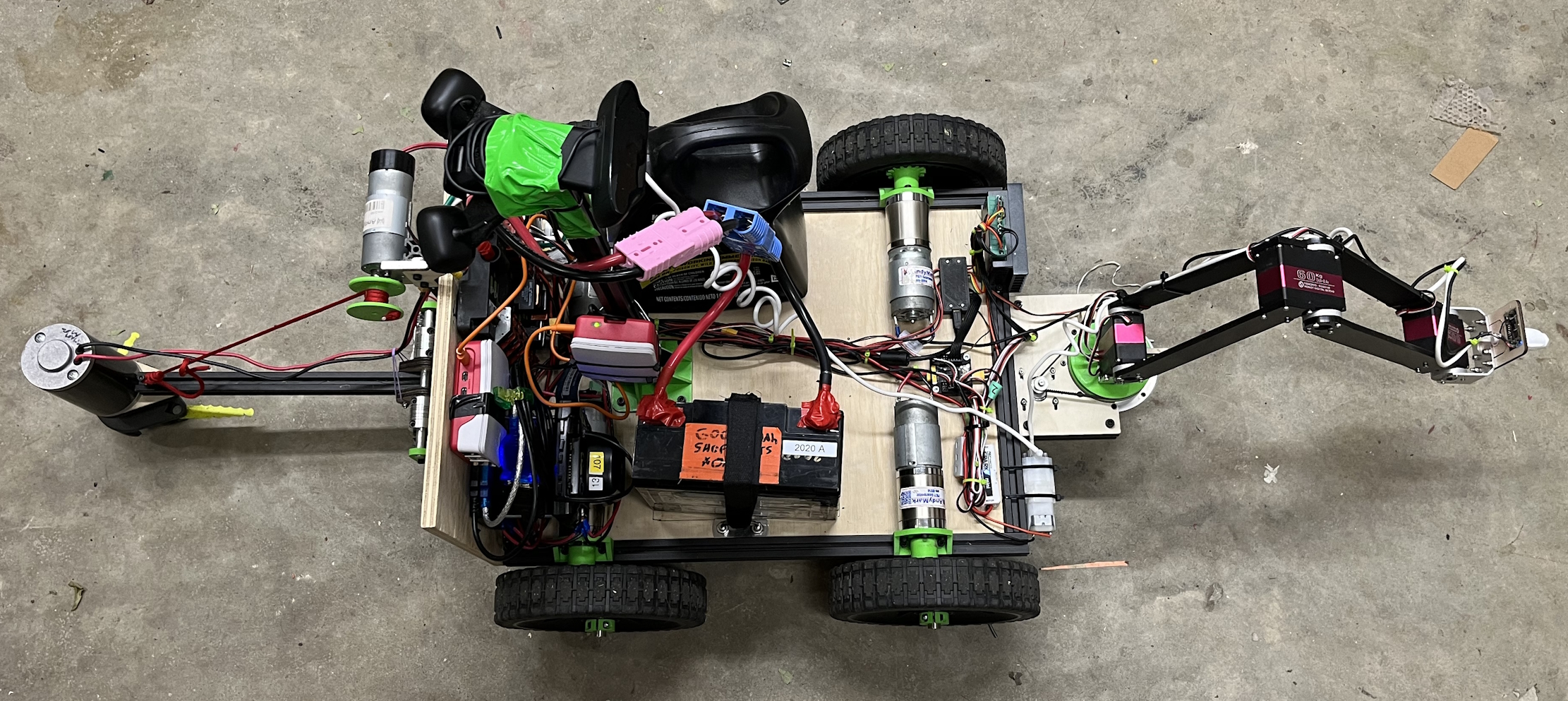